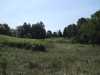
June 2003
|
The first view from the
street of the property located at 221A Richmond Street in
Sandhurst. It is a five acre parcel with 363 feet of shoreline
frontage, with sandy beach (small and comes and goes with
the wave action) and pebbles, stones, and boulders. The water is not
visible through the undergrowth.
|
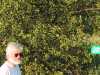
July 2003
|
Michael and part of the
street number sign.
|
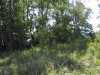
June 2003
|
The shoreline is wildly
overgrown with underbrush and willows and ash trees. The trees were in
strong competition with each other, and needed to be thinned out to
provide room for the
important ones to thrive, and to provide a view of the water, which is
almost totally obscured.
|
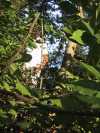
July 2003
|
Diane in the foliage at
the east end of the shoreline. This is what the brush
and undergrowth was like before it was cleared out.
|
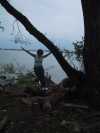
August 2003
|
Exultant Diane, by the
large willow, with some of the wood from the cleared trees.
|
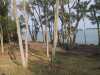
August 2003
|
An arborist ("A Cut
Above") was engaged to clear the underbrush, thin the trees, and trim
the remaining trees. This was a huge job as there were large fallen
willow trunks in several places. The view of the water looks to the
Western Gap between Amherst Island and the eastern end of Prince Edward
County.
|
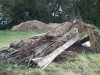
August 2003
|
There was a lot of rubbish
in the undergrowth, mostly from the cottage that was on the earlier
severed lot, and at sometime in the past had been cleared off the
property, and precipitating the return of this parcel to the larger one.
|
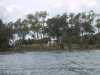
August 2003
|
From the
kayaks it was possible to appreciate the topography of the
property from the water. It is possible to see that the central portion
of the shoreline is bracketed by a section at either end left as a
buffer with the neighbouring properties. |
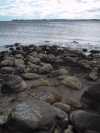
August 2003
|
Adjacent to the "sandy"
beach where the kayaks are launched is this
spread of granite glacial boulders running out into the water. Opposite
the eastern end of Prince Edward County is visible with a part of the
Western Gap. |
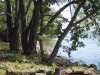
August 2003
|
The willows follow the
stony shore berm, providing shade. Looking to the east.
|
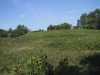
August 2003
|
The property has three or
four knolls, that make it rather distinctive in relation to the
surrounding landscape which is quite flat. Hence the name Sandhurst,
with "hurst" meaning "hillock". These are the only hillocks in the
immediate area.
|
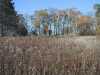
November 2003
|
View of the Anglican
Church on Bath Road from the small knoll.
|
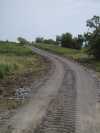
July 2004
|
The road into the building
site take you over the top of the big knoll, seen above. The contractor
for the road, septic bed, etc. is George Benn and Sons.
|
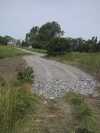
July 2004
|
The end of the road where
the house will be sited.
|
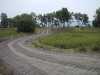
July 2004
|
The road from the top of
the big knoll, looking towards the shoreline.
|
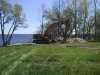
July 2004
|
Making the shorewell by
blasting. Contractor Frank's Drilling and Blasting, Newburgh. |
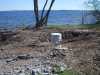
July 2004
|
The shorewell.
|
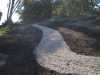
October 2004
|
The path parallel to the
shoreline. It can be approached from the front of the house.
|
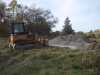
November 2004
|
Preparing the bed for the
hydronic floor. Contractors are Wemp and Smith.
|
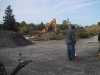
November 2004
|
Levelling the bed for the
hydronic floor.
|

November 2004
|
The tile bed for the
septic system.
|
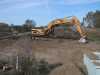
November 2004
|
Dressing the tile bed for
the septic system.
|
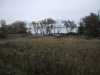
November 2004
|
A view of the house site
from the top of the big knoll.
|
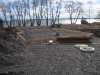
November 2004
|
The form work for the
footings seen at the garage entrance.
|
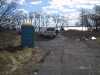
November 2004
|
Temporary plumbing! |
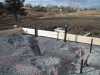
November 2004
|
Placing the plumbing lines
under the floor. |
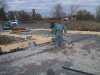
November 2004
|
The plumbing contractor is
Brunet of Kingston.
|
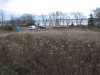
November 2004
|
A view of the site with
the footing forms in place from top of the big knoll.
|
November
2004 |
The trench for the
waterline from the house to the shorewell.
|
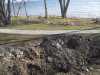
November
2004
|
The waterline with a view
of the path with the germinating grass.
|
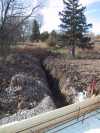
November 2004
|
The trench for the hydro
service. At the far end the excavator encountered a spring that would
have served for a well!!
|
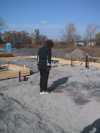
November
2004
|
Diane pacing out the
measurements.
|
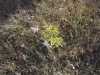
November
2004
|
One of the pine seedlings
planted in the spring. The oaks, larches and pines seem to have had a
good start in the cool and moist summer.
|
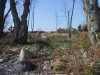
November
2004
|
A view of the house site
from the shoreline. Follow the path.
|
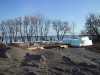
November
2004
|
The floor insulation ready
to be installed.
|
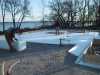
November
2004
|
Installing the floor
insulation.
|
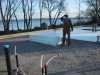
November
2004
|
Is it really a puzzle?
|
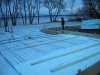
November 2004
|
The reinforcing mesh was
placed November 11.
|
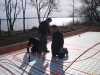
November 2004
|
The hydronic floor heating
relies upon loops of tubing in the concrete floor. McKeown and
Wood are the contractors.
|
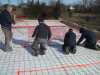
November 2004
|
This was a warmer, sunny
day, so warm that the installers were remarking on how hot it was
getting by 11 a.m., although the previous evening the temperature went
down to -9 C.
|

November 2004
|
When this stage is
completed, the floor is ready to be poured along with the footings. The
footings are "warm," which avoids the need for deep frost walls.
|
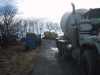
November 2004
|
The footings and floor
being poured. The crew started at 7 a.m. intending to work into the
evening if necessary to finish the surface.
|
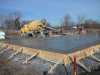
November 2004
|
The footings and floor
used about 50 cubic yards of concrete.
|
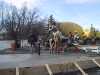
November 2004
|
Pouring the footings and
floor. The main house area is complete. The garage is still to be
done.
|
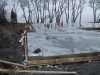
November 2004
|
Two days after the slab
was poured, the forms are stripped off in preparation for the
application of rigid insulation along the edges. It had rained
overnight, and the pools of water show that the slab is quite level,
but not perfect. This is a view from the garage entrance.
|
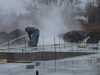
November 2004
|
It seems odd to "cut" the
slab after so much trouble has been taken to get a smooth surface. It
is assumed that all massive floors of concrete will want to crack
somewhere. By cutting the slab surface to a depth of about one inch,
the cracking will be directed along the weak points established by the
cuts. However, it may never crack! This is a preventative measure to
direct unsightly cracks in an orderly way.
|

November 2004
|
The hydro line will be
underground. This seemed a good idea until a spring was discovered near
the pole. Nevertheless, Hydro One said to proceed as planned in the
layout (Plans).
|
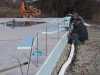
November 2004 |
The perimeter of the slab
is insulated with "PolyVert," a 'greener' form of rigid insulation.
The choices of material throughout lean to the sustainable, green
category. The perimeter drainage is visible in this photograph, and
will be covered with gravel and sand.
|
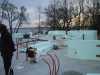
November 2004
|
The Insulated Concrete
Form (ICF) system selected for the walls is the Nudera product. It was
selected because Nudera promoted an integrated building system,
including floor and ceiling insulation systems. The latter proved to be
too expensive compared to conventional insulation. Nevertheless, the
wall system is very efficient and easy to put up to receive the
concrete.
|
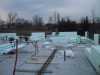
November 2004
|
The placement of the
exterior walls defines the interior space in a dramatic way.
|
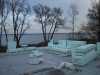
November 2004
|
The Nudera forms are
unique in that they are somewhat like an accordion, and fold up for
shipping, and unfold for installation.
|
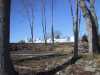
November 2004
|
A view from the shoreline
of the concrete forms being put in place. The previous two days were
too rainy and windy to work on the site.
|
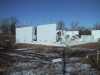
November 2004
|
A view from the south-west
of the wall forms approaching their maximum height.
|
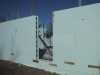
November 2004
|
A close up of the west
wall and a window cut-out. The windows are close to the floor and
life-size so from the inside it will seem possible to move out on the
same level (but of course it is a window!).
|
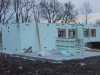
November 30, 2004
|
From the garage entrance,
walls at full height.
|
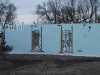
November 30, 2004
|
From the east end, walls
at the full height.
|
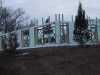
November 30, 2004
|
From the south-east, walls
almost at full height.
|
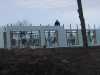
November 30, 2004
|
Facade from the shore,
walls partially completed to full height.
|
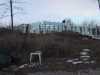
November 30, 2004
|
View from the sandy beach.
|
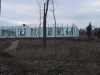
November 30, 2004
|
View from the shoreline.
|
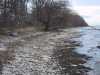
November 30, 2004
|
Looking east on the
shoreline, low water.
|
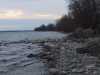
November 30, 2004
|
Looking west on the
shoreline, low water.
|
>>>>>>>>>>>>
>>>>>>>>>>>>
|
Go
to December Progress
To go to the March page.
|